General
Requirements to refrigerants. Before considering characteristics of refrigerants, let's settle on basic requirements toward them. Requirements to refrigerants are divided into the following groups:
- Ecologic - ozone-safety, low global warming potential, incombustibility and non-toxicity;
- Thermodynamic - big bulk cold-productivity; low boiling point at atmospheric pressure; inferior condensing pressure; good thermal conduction; low refrigerant firmness and tenacity ensuring reduction of hydraulic loss for friction and local resistance while its transportation; maximum proximity to substituted refrigerants (for alternative ozone-safe refrigerants) with regard to pressures, temperatures, specific bulk cold-productivity and refrigerative coefficient;
- Operational - thermal stability, chemical compatibility with materials and refrigerative oils, ample mutual dissolubility with oil to ensure its circulation, technological effectiveness of the use; incombustibility and non- explosion-proof; ability to dissolve water, insignificant fluidity; availability of flavor, colour, etc. ;
- Economic - availability of commodity production, moderate (low) prices.
It is almost impossible to find refrigerants meeting all the listed requirements, that's why, in any specific case refrigerants are selected with account of concrete conditions of a refrigerating facility operation, preference should be given to those ones satisfying fundamental and determinant requirements.
Alternative substances can be pure (simple) substances and blends. Preference is given, first of all, to pure substances.
Peculiarities of thermodynamics of refrigerative blends. In molecular theory of solutions, they distinguish zeotrope and azeotrope blends.
Thermodynamic activity of a blend of azeotrope composition is similar to the activity of a pure substance because the composition of its gas and liquid phases is the same, and pressures at condensation and boiling points coincide.
Concentrations of gas and liquid phases of zeotrope blend under conditions of thermodynamic balance are differed, and isotherm under coexistence curve in p--h-coordinates has a slant, that is, boiling at constant pressure occurs while increasing of the refrigerant temperature from t01 to t02, and condensation - while temperature dropping from tK1 to tK2 (Fig.). It is necessary to take into account when determining the level of steam overheat at the compressor entry, as well as when evaluating energetic characteristics of a refrigerating facility.
Thus, boiling point and condensation point should be determined another way. Boiling point is calculated as an average temperature t0 between dewpoint temperature t02 at constant suction pressure pBC and temperature when a refrigerant comes into evaporator t01.
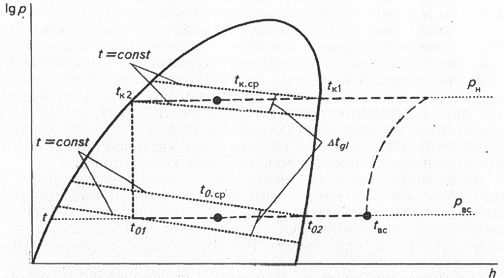
Condensation point is calculated as an average temperature tK.CP between dewpoint temperature tK1 (temperature of the beginning of condensation process at constant discharge pressure pH) and temperature tK2 of the liquid at the condenser exit. Difference of phase transfer temperatures at constant pressure (at boiling and condensation) got the name Dtgl or temperature glide. Value Dtgl depends on composition of the actuating medium and is an important technological parameter.
Overheat of intake steam is calculated as common difference of temperature tBC at the compressor entry and dewpoint temperature t02 of the refrigerant at suction pressure pBC. When regulating cold-productivity of refrigerating facilities with the help of adjusting faucets, all the above-stated has to be taken into account.
Liquid aftercooling is calculated as common difference between actual liquid temperature and temperature of condensation end point tK2 at discharge temperature pH.
When controlling pressure, it is especially important to take into account temperature glide of a blend of refrigerants, for example, such refrigerants as 407C, R410A and others. Moreover, temperature glide is a governing factor when determining the size of heat-exchange apparatus.
Pressure loss in the system considerably increases temperature glide. Neglect of this phenomenon when making up heat balance can cause understatement of sizes of heat-discharge apparatus and other elements of the refrigerating system. Influence of this factor is especially significant when the refrigerating system is operated at the breaking point of its possibilities.
Thus, zeotrope blends have their advantages and disadvantages. On the one hand, changing of composition of the actuating medium during its circulation along the refrigerating system boundary can cause increasing of cold-productivity and refrigerative coefficient as compared to these characteristics for pure refrigerants. On the other hand, using of zeotrope blends causes reduction of heat transfer rate in the evaporator and condenser.
One more disadvantage of zeotrope blend is potential possibility of its composition change when appearing leakage in the refrigerating system boundary, which affects fire safety and cold-productivity of the facility. In order to reduce probability of composition change in the area of concentrations where the fire risky component prevails, they add to the blend an incombustible component whose saturated vapor pressure is close to the pressure of fire-risky component vapors or higher than that. If the blend contains even one combustible component, it is necessary to avoid air intake into the system when charging.
Basic mechanisms of changing of multi-component refrigerant composition in the refrigerating facility are the following:
- Vapor-fluid separation of zeotrope blends in the compressor and heat-exchane apparatus;
- Different dissolubility of the blend components in refrigerating oil;
- Selective loss of any component due to the component leakage because of the system nonhermeticity; changing of mass of a multi-component actuating medium in separate elements of the refrigerating system at different thermal loads.
While practical using of zeotrope blends, it is recommended:
- To charge the refrigerating system from a ballon filled with fluid refrigerant;
- Blends with distinctly expressed temperature glide should not be recommended for using in refrigerating facilities with flooded evaporator;
- To take into account different dissolubility of each component of the blend refrigerant in refrigerative oils;
- When calculating characteristics of a refrigerating facility it is necessary to take into account changing of a multi-component refrigerant composition.
Designations of refrigerants. In Russia there has been introduced the International standard ISO-817 "Organic refrigerants", according to which there have been presupposed digital designations of refrigerants in technical documentation for refrigerants and oils.
The standard allows several designations of refrigerants: symbolic, trade (brand), chemical and chemical formula. Designations of main refrigerants are given in Appendix 19.
Symbolic designation of refrigerants is preferable and consists of letter "R" or word Refrigerant and combination of figures. For example, chladone-12 has R12 (CF2Cl2). Figures can be interpreted depending on chemical formula of a refrigerant. The first figure (1) points out methanoic row, the next figure (2) fluorine atoms corresponds to the quantity in the contexture. In case when hydrogen in methane derivatives is displaced not completely, to the first figure there's added the quantity of hydrogen atoms remained in the contexture, for example, R22.
For ethane row, first there is put down the combination of figures - index mark equal to 11, for propane - 21, for butane - 31. For these derivatives, they add to the second figure a number of hydrogen atoms if they are available, for example, trifluorotrichloroethane C2F2Cl3 - R113.
In case if in the contexture composition there is bromine, in its designation letter "B" appears followed by a number of bromine atoms, for example, R13B1 - trifluorobromine methane, chemical formula CF3Br.
Isomers of ethane derivatives have the same combination of figures (digital index), and the fact that this isomer is absolutely symmetrical is reflected by its digital index without any revision. As considerable asymmetry increases, letter "a" is added to the digital index of the corresponding isomer, in case of bigger asymmetry it is substituted by letter "b", then "c", for example, R134a, R142b etc.
The manner of digital designation of unlimited hydrocarbons and their halogen-derivatives is analogous to the one considered above, but to the figures positioned after letter "R" 1 is added from the left for designation of thousands (for example, R1150).
For refrigerants on the basis of cyclic hydrocarbons and their derivatives, letter "C" is inserted after letter "R" before the digital index (for example, RC270).
Refrigerants of non-organic origin have numbers corresponding to their relative molecular mass, plus 700. For example, ammonia, whose chemical formula is NH3, is designated as R717, water (H2O) - as R718.
Refrigerants of organic origin are assigned family 600, and the number of a refrigerant within this family is assigned arbitrarily (for example, emthylamine has number 30, therefore, its designation will be R630).
Zeotrope, or non-azeotrope blends, are assigned family 400 with arbitrary number for each refrigerant within this family, for example, R401A.
Refrigerants on the basis of paraffin hydrocarbons containing bromine have double designation. This designation has letter "B" in its composition, for example, R13B1, or letter "H", followed by figures 1 and 3, but then two more figures are added, the first of which points out the quantity of chlorine atoms, the second one - the quantity of bromine atoms. For example, trifluorobrominemethane (CF3Br), whose quantity of chlorine atoms is 0, and bromine atoms - 1, can be designated both R13B1, or H1301.
At present there appeared a tendency while designating refrigerants to anticipate digital index not with letter "R" or "H", but with abbreviation indicating directly the group to which the refrigerant is related depending on its level of influence on the environment. For example, the following designations are suggested:
- CFC12 for R12 refrigerant, related to CFC group, which includes refrigerants harmful for the environment;
- HCFC125 for R125 refrigerant, related to HCFC group, containing refrigerants less harmful for the environment;
- HFC134a for R134a refrigerant, related to HFC group, containing refrigerants harmless for the environment.
Each company - producer of refrigerants releases for sales its own products under personal name, for example:
"MackDown Chemical Inc" - MackFri®, "Du Pont de Nemour" - Freon or SUVA®, "Elf Atochem" - FORANE®, "Solvay" - Kaltron, "Montedison" - Algofrene, AZSO - Allied Signal, ICI - Klea, "Daikin Kogyo" - Daiflon.
Therefore, R407C, for example, can come into the market under the brands MackFri®-07c, FORANE® 407C, SUVA® 9000 and others.
|